Rabat’s recent announcement that it would soon sign an agreement for the construction of a “gigafactory” to make electric vehicle (EV) batteries has placed Morocco in pole position to become a green mobility leader in the Middle East and North Africa. A development of enormous significance for the kingdom, Morocco’s rise as a global-scale, EV manufacturing hub is as critical to Western supply chain resilience as it is to promoting carbon-free mobility to combat climate change. The focus on shortening supply chains to ensure the stability of European consumer markets has already fueled the rapid advance of Morocco’s automotive manufacturing sector and its development of more advanced manufacturing processes. Now, Morocco’s reserves of critical battery minerals are accelerating its entrance into EV manufacturing. With ample solar and wind energy resources along with utility-scale infrastructure already in place to utilize them, Morocco has the potential to drive a green mobility revolution by powering the production of EVs using renewable energy.
Nearshoring: The driving momentum behind Moroccan EV manufacturing
On July 21, 2022, Moroccan Minister of Industry Ryad Mezzour informed the press that the kingdom was close to signing a deal with EV battery manufacturers to establish a massive local production facility. Without identifying any company, Mezzour said the plant would be a gigafactory and that Rabat hopes to sign a $2 billion deal for the plant before the end of this year. A term popularized by the pioneering American EV manufacturer Tesla, a gigafactory is an extremely large-scale battery manufacturing plant in which each production line has an annual output of around 3 gigawatt-hours (GWh) of lithium-ion (Li-ion) battery cells, sufficient to make batteries for 30,000-45,000 EVs, depending on the size and the model. While Mezzour has been vague about the number of lines and total capacity of the proposed Moroccan facility, Tesla’s successful $2 billion gigafactory in Shanghai, China, was originally intended to produce 500,000 EV batteries per year. It is possible that the output of Morocco’s gigafactory will be of a comparable order of magnitude.
The production of EV batteries on such a scale would be appropriate for Morocco’s impressive automotive manufacturing ecosystem, which already has the capacity to produce over 700,000 vehicles per year. Now Rabat is aiming to increase Morocco’s output to 1 million vehicles per year by 2025, with many of those being EVs. Already in November 2021, Morocco’s public finance bill for 2022 proposed a reduction of the import duty on lithium-ion cells from 40% to 17.5% to promote the local assembly of Li-ion batteries using cells imported from East Asia. The key to Morocco’s rise as a green mobility manufacturing giant will be expanding its automotive ecosystem to include local manufacture of Li-ion batteries, which represent 30% to 40% of the cost of the average EV. The new gigafactory could thus accommodate producing the targeted additional 300,000 vehicles as EVs.
Nearshoring, combined with Rabat’s smart industrial planning and careful cultivation of foreign partnerships, is the engine of the self-reinforcing momentum propelling the advancement of Morocco’s automotive manufacturing sector. During the years immediately prior to the outbreak of the COVID-19 pandemic, global supply chains were already starting to shorten as companies and countries placed greater emphasis on resiliency than on the immediate cost efficiency of just-in-time inventories delivered from distant points across the globe. For Europe, this structural transformation meant bringing sourcing and manufacturing closer to European end-markets. In order to maintain a competitive advantage in operating expenditures, international firms began to locate manufacturing facilities in Morocco.
Rabat fueled the momentum for nearshoring in Morocco through its 2014-2020 Industrial Acceleration Plan and its concurrent development of high-speed, high-volume capacity transportation that saw the construction of Tanger Med Port, the Mediterranean’s largest, as well as the al-Boraq rail line (Casablanca–Tangier), Africa’s first high-speed rail system. Morocco’s linked state-of-the-art port and rail prompted Groupe Renault to establish a second Moroccan manufacturing plant and Groupe PSA (now part of the Stellantis conglomerate) to open a Peugeot manufacturing plant in Kénitra, north of Rabat. The Renault and Peugeot plants are supported by approximately 250 international suppliers from the U.S., Europe, Japan, and elsewhere that operate their own local manufacturing plants. For example, the Chinese firm CITIC Dicastal, the global leader in aluminum cast parts, built a $400 million plant in Kénitra that can produce 6 million pieces annually to supply Peugeot.
As a result of the nearshoring momentum, Europe’s two best-selling car models — the Peugeot 208 and Renault’s Dacia Sandero — are made in Morocco. Now, Rabat has its sights on manufacturing their EV versions. Starting in 2020, Renault shifted its entire production of the Dacia Sandero from Romania to the company’s plants in Casablanca and Tangier, where labor costs can be up to 50% lower. In 2021, Renault launched its Dacia Spring EV model in Europe, marketing it as the continent’s cheapest electric car. The car is manufactured by Renault in China, home to CATL — the world’s leading producer of EV Li-ion batteries, whose global market share reached 35% in the first quarter of 2022. The production of EV batteries in Morocco, with at least some of the major battery metals sourced locally, could represent a sufficient cost advantage to convince Renault to build the Dacia Spring or successor EV models at the company’s Moroccan plants. Prioritizing supply chain security for its European end-markets over just-in-time inventories supplied by East Asia, Renault would likely start EV production in Morocco once Li-ion battery manufacturing gets under way.
Stellantis, the parent company of Peugeot, is ahead of Renault. Peugeot’s Kénitra plant, established in 2019, manufactures the gas-powered version of the Peugeot 208. Since the all-electric Peugeot e-208 uses the same chassis, Moroccan EV battery production could incentivize Stellantis to shift production of the e-208 from Slovakia to its facility in Kénitra, likewise benefiting from labor cost reductions. Indeed, Stellantis’ German auto manufacturing subsidiary Opel has already initiated production of its Rocks-e EV model in Kénitra, at the plant of its sister company Peugeot. Morocco geared up for the move by developing semiconductor production capacity for EV microchips. Franco-Italian STMicroelectronics, Europe’s leading integrated device manufacturer, operates a sizeable automotive chip production facility in Bouskoura, on the outskirts of Casablanca and connected by rail link to the rest of the country’s auto manufacturing chain. In 2021, the company inaugurated a new production line in Morocco to manufacture electronic chips for Tesla.
Close is beautiful: Morocco’s cobalt reserves contribute to EV battery breakthrough
Li-ion batteries, the basis of modern EVs, require expensive and difficult-to-obtain metals, primarily lithium and cobalt, to discharge their electric current. A lithium-based compound acts as the anode, which donates the electrons that flow through the system, while the cobalt-based compound acts as the cathode to receive the electrons. The most common EV batteries are the energy-dense batteries that use a nickel manganese cobalt (NMC) cathode or sometimes a nickel cobalt aluminum (NCA) cathode. Energy dense Li-ion batteries with cobalt generally enable EVs to have longer driving ranges between charging.
Cobalt availability is a limiting factor for the widespread diffusion of passenger EVs. While a cellular phone battery requires 0.2-0.4 ounces (5-10 grams) of cobalt, an electric car battery requires 10-20 pounds (22-44 kilograms). Currently, there are about 12 million electric passenger cars on the road worldwide, but the number is expected to jump to 54 million as early as 2025, increasing the demand for cobalt. Over 50% of the world’s reserves of this crucial metal are located in the Democratic Republic of the Congo (DRC), which currently produces 70% of the world’s mined cobalt. China, the largest EV battery maker, is also the leading producer of refined cobalt, accounting for about 65% of the global output. Beijing seeks to dominate the DRC’s mining of the highly strategic metal, and, accordingly, Chinese production of mined cobalt in the DRC is expected grow 60% by 2024, compared to 2020.
Cobalt extraction in the DRC is so-called artisanal and small-scale mining (ASM), conducted under harsh and toxic conditions by around 255,000 Congolese citizens using their own rudimentary tools and hands; among these workers are 40,000 children as young as 6 years old. Western technology companies and EV manufacturers are under increasing pressure to ensure that the cobalt they use is produced from safe and sustainable mining practices.
Geopolitical competition with China over supply chains, coupled with environmental, social, and governance concerns, are leading Western-headquartered EV manufacturers in particular to look for closer and less ethically problematic suppliers of cobalt. The need is intensified by the fact that Europe is likely to be one of the centers of immediate EV market growth, spurred by the European Commission’s July 2021 directive to phase out all fossil fuel-powered vehicles in the European Union by 2035. Similarly, Morocco cannot afford to lose its European market. As Industry Minister Mezzour explained, “Morocco has no choice, because 90% of our automotive exports go to Europe and Europe has decided to switch to all-electric by 2035.”
Province. Photo courtesy of Managem.
The proximity of Morocco’s cobalt reserves to European EV manufacturing centers, which face high demand pressure for this critical metal and the ability to ensure that it is extracted through more palatable mining practices, has thus turned their attention to North Africa. This is despite the fact that Moroccan cobalt reserves are relatively small: only the world’s 11th largest. In 2020, the kingdom’s cobalt exports totaled $84 million, ranking Morocco the 13th-biggest exporter. Nonetheless, in July 2020, German automaker BMW signed a $113 million contract with Moroccan mining company Managem to supply 20% of the cobalt required to manufacture BMW’s next-generation electric drive trains. Renault, on June 1, 2022, signed a contract with Managem to supply 5,000 tons of cobalt sulfate annually for seven years. As the purchasing director for Renault explained, the deal with Morocco ensures “a supply closer to our ecosystem of manufacturing electric batteries in Europe.” Considering that Managem is supposed to start supplying cobalt to Renault in 2025, the company may also be eyeing local battery production in Morocco.
A further incentive for Renault is that the cobalt supplied by the North African state is expected to have a low carbon footprint, with up to 80% of the energy for production coming from renewable sources. The company has set carbon reduction goals for its EV batteries of 20% by 2025 and 35% by 2030, compared to 2020. The reduction in the carbon footprint of Morocco’s cobalt supply will also be achieved through the recycling of end-of-life batteries. Global mining and metal trading giant Glencore entered into a partnership with Managem in January 2022 to produce recycled cobalt from disused lithium-ion batteries at Managem’s hydrometallurgical refining facilities operated by its subsidiary Compagnie de Tifnout Tighanimine (CCT), about 23 miles (37 kilometers) from Marrakech. Glencore will provide CCT with so-called black mass, processed from dismantled and shredded Li-ion batteries. In addition to cobalt, the partnership is also seeking to extract lithium carbonate and nickel hydroxide from the black mass supplied by Glencore. If extracted in sufficient quantities, Morocco could locally source all of the major metals used in NMC Li-ion batteries.
The kingdom possesses small nickel and manganese reserves that could supply domestic NMC cathode manufacturing. And Morocco may have its own domestic supply of lithium as well. Moroccan media reported in May 2022 the discovery of significant deposits of this alkali metal in the country’s disputed Sahara region near the Mauritanian border.
Morocco’s phosphate reserves turbocharge EV battery manufacturing
Morocco’s massive phosphate reserves are a critical factor in its transformation into a global-scale, EV battery production hub. A growing trend in electric passenger cars is to replace NMC Li-ion batteries with lithium iron phosphate (LFP) batteries, substituting expensive cobalt and nickel as well as manganese for relatively cheaper phosphate and iron. While not providing the same longer driving ranges as NMC batteries, phosphate-based LFP batteries are less expensive, safer, and last longer than their cobalt-based counterparts. The increasing utilization of LFP batteries favors Morocco for EV battery production as the country sits on over 70% of global phosphate rock reserves and is the world’s second-largest phosphate producer, after China.
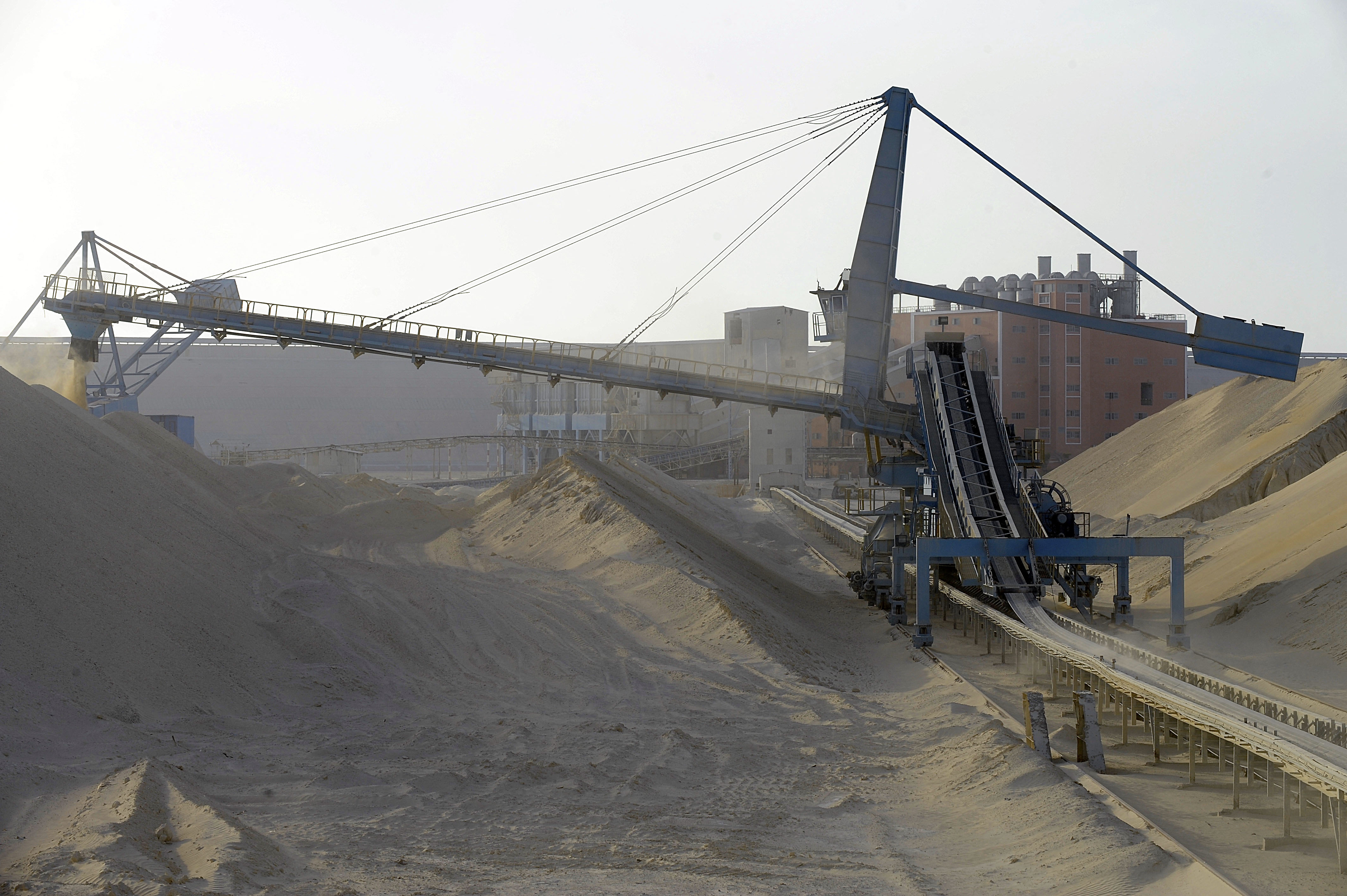
Morocco’s phosphate mining sector was established in 1921 to provide a source of phosphorus primarily for the manufacture of synthetic fertilizers. The kingdom’s massive phosphate mining and fertilizer manufacturing sector, run by the state-owned OCP Group (formerly Office Chérifien des Phosphates), has transformed Morocco into a gatekeeper of the world’s food supply. During the 1980s and 1990s, OCP began manufacturing phosphoric acid (H3PO4), the chemical input to phosphorus-based fertilizer, and the fertilizer itself. Phosphoric acid is also the input to make iron (II) phosphate Fe3(PO4)2, an iron salt of phosphoric acid. The iron (II) phosphate can then be used to make lithium iron phosphate (LiFePO4), now the increasingly preferred material for Li-ion cathodes in EV batteries.
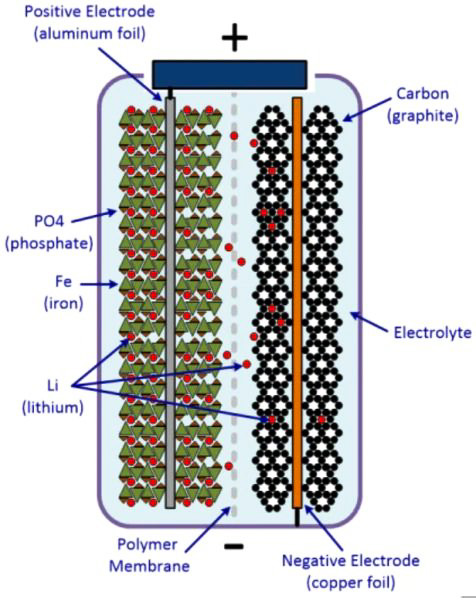
(LFP) battery. Image courtesy of Skill-Lync.
By using phosphate and iron — Morocco is also a net exporter of iron ore — to make LFP batteries, instead of nickel, manganese, and cobalt for its NMC counterpart, Morocco could enjoy a cost advantage of upward of 70% per kilogram. Moreover, iron phosphate is nowhere near as toxic as cobalt oxide or manganese oxide. The LFP batteries have a longer cycle life, with a slower rate of capacity loss compared to NMC batteries. And LFP batteries are much safer as well: With higher thermal stability, LFP batteries emit significantly less heat than NMC batteries and are not as susceptible to exploding or igniting when an EV is misused or suffers physical damage.
Due to these advantages, Tesla announced in its Q3 2021 report, “For standard range vehicles, we are shifting to Lithium Iron Phosphate (LFP) battery chemistry globally.” In speaking to the Moroccan press, Industry Minister Mezzour indicated that Morocco was looking at producing stationary batteries for the storage of renewable energy as well as for EV batteries. These stationary Li-ion batteries bear a clear resemblance to Tesla’s “megapack” line of utility-scale energy storage units that the company launched in 2019, suggesting that Tesla may be one of the international firms in negotiations with Morocco for the gigafactory.
Conclusions
In 2020, OCP mining operations produced 40.7 million tons of phosphate and exported 10.3 million tons of the raw material. From its phosphate supplies, OCP Group manufactured 7.1 million tons of phosphoric acid, exporting 1.9 million tons of the key input. Morocco will need to expand its phosphate and phosphoric acid production to make LFP EV batteries. In response to the global shortage of fertilizer due the Russo-Ukrainian war, OCP announced on May 17 that it would increase its 2022 fertilizer production by 10%, putting an additional 1.2 million tons on the global market. The figure reflects OCP’s ability to create a 1-million-ton-capacity fertilizer production line in six months, which entails commensurate increases in phosphate and phosphoric acid production.
For Morocco, the diversification of uses and markets for its phosphate output is highly desirable. At the same time, Rabat bears a responsibility to ensure that OCP does not develop insufficient phosphate production capacity, which would result in demand pressure competition between LFP batteries and phosphorus fertilizers, thus driving up fertilizer prices and consequently increasing the level of global food insecurity. Morocco’s Western partners, especially those whose companies are involved in the kingdom’s LFP battery production, should encourage and support Morocco to develop spare capacity in its phosphate sector. Analogous to the role Saudi Arabia’s Aramco plays in stabilizing oil markets, Morocco’s OCP should have the ability to bring spare phosphate production capacity online and take it offline as needed.
Morocco possesses considerable solar and wind resources. Phosphate production as well as other parts of Morocco’s EV manufacturing chain should become increasingly powered by renewable energy to ensure that its green mobility vehicles are produced in a sustainable and climate smart manner. OCP covers 89% of the energy needs for its phosphate and phosphorus fertilizer production through co-generation (re-using exhaust energy to create cleaner and cheaper power from fossil fuels) and renewable sources. It plans to eventually cover 100% of its energy needs in this manner. Reliant on gas and coal imports, Morocco’s Western partners should work with Rabat to move the country’s EV manufacturing to be powered by locally available solar and wind resources to promote greater supply chain resilience as well as ensuring that its manufacture of green mobility vehicles is also green.
Professor Michaël Tanchum is a non-resident fellow with the Middle East Institute's Economics and Energy Program. He teaches at Universidad de Navarra and is a senior fellow at the Austrian Institute for European and Security Policy (AIES). You can follow him on Twitter @michaeltanchum. The author would like to thank Rocco Schwerfel for his research assistance.
Photo by BALINT PORNECZI/Bloomberg via Getty Images
The Middle East Institute (MEI) is an independent, non-partisan, non-for-profit, educational organization. It does not engage in advocacy and its scholars’ opinions are their own. MEI welcomes financial donations, but retains sole editorial control over its work and its publications reflect only the authors’ views. For a listing of MEI donors, please click here.